Applying an epoxy coating to concrete is not as simple as it seems. One crucial step often overlooked is checking the concrete for moisture before applying the epoxy coating, also known as moisture testing.
This process is really important, as it ensures that the concrete is dry enough for the epoxy to adhere properly. If not, the coating may peel or bubble over time, ruining the quality and longevity of your coating. In this guide, we’ll delve into the importance of moisture testing, how to conduct it, and the implications of moisture presence for epoxy applications.
Table of Contents
The Importance of Moisture Testing in Concrete
Moisture testing is a critical step in preparing concrete for an epoxy coating. It helps identify if the concrete is dry enough for the epoxy to adhere properly. Too much moisture can lead to peeling, bubbling, or even mold and mildew growth underneath the epoxy.
Moreover, moisture testing is not just about ensuring a successful epoxy application. It’s also about avoiding costly repairs or replacements down the line. By conducting a thorough moisture test, you can ensure the longevity of your epoxy coating and the overall quality of your concrete surface.
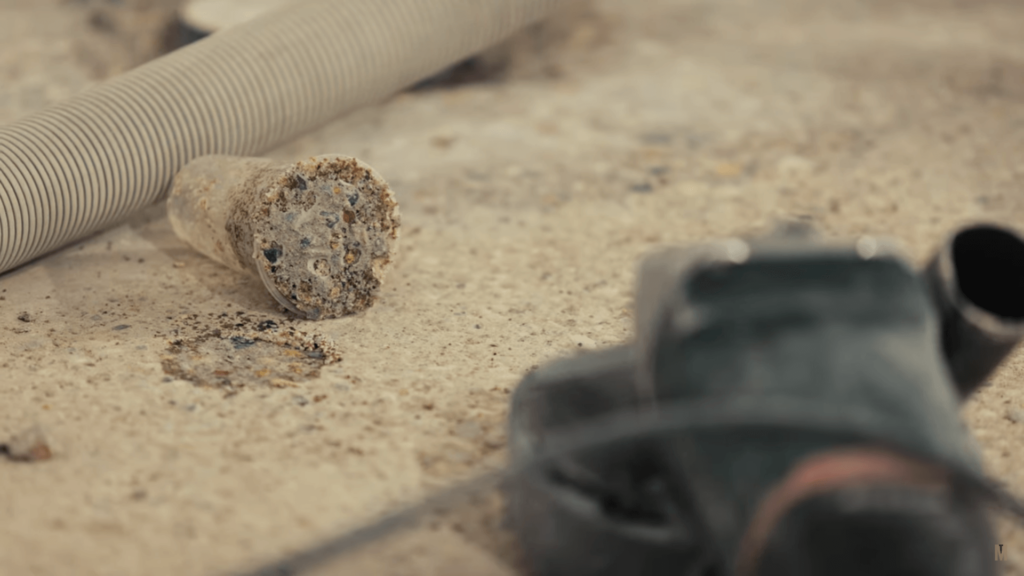
The Effect Moisture Has on Epoxy Adhesion
Epoxy is a type of coating that bonds tightly to concrete surfaces. However, its adhesion can be significantly affected by moisture. When moisture is present in the concrete, it can interfere with the bonding process. This can lead to a weak bond between the epoxy and the concrete. As a result, the epoxy may peel or bubble up over time. This not only affects the appearance of the surface but also its durability and functionality.
Common Moisture Testing Methods for Concrete
There are several methods to test the moisture content in concrete. Each method has its advantages and limitations.
The most common methods include the calcium chloride test, the use of moisture meters, and relative humidity (RH) testing. These methods provide different types of information about the moisture content in the concrete.
Calcium Chloride Test
The calcium chloride test is surface-based. It measures the moisture vapor emission rate (MVER) from the surface of the concrete. This test is widely used due to its simplicity and cost-effectiveness. However, it only provides information about surface moisture, not the moisture content deeper within the slab.
Moisture Meters
Moisture meters are handheld devices that measure the moisture content in concrete. They work by sending an electrical signal into the concrete and measuring the resistance. Then the resistance is converted into a moisture content reading. However, these readings can be affected by other factors such as concrete density and temperature.
Relative Humidity (RH) Testing
Relative humidity (RH) testing is considered the most accurate method for measuring moisture in concrete. It measures the moisture conditions deep within the slab, not just at the surface. This test involves drilling a hole into the concrete and inserting a probe to measure the RH level. It provides a more comprehensive understanding of the moisture conditions within the concrete slab.
Conducting a Calcium Chloride Test
The Calcium Chloride test is a common method for testing concrete moisture. It involves measuring the amount of moisture vapor emitted from the concrete surface over a specific period.
First, the concrete surface is cleaned and a small area is sealed off with a plastic dome. Inside this dome, a dish of calcium chloride is placed to absorb moisture. Then after 60 to 72 hours, the dish is removed and weighed. The weight gain indicates the amount of moisture absorbed, which is then used to calculate the moisture vapor emission rate.
This test provides a snapshot of the moisture condition at the time of testing. It’s important to note that results can vary based on environmental conditions and concrete properties.
Interpreting Moisture Test Results and Next Steps
Once you have the results from your moisture test, it’s time to interpret them. The moisture vapor emission rate obtained from the Calcium Chloride test, for instance, is usually expressed in pounds per 1,000 square feet per 24 hours. If the emission rate exceeds the tolerance level recommended by the epoxy manufacturer, it would be a good idea to delay applying your coating. Instead, focus on moisture reduction options like the use of vapor barriers or dehumidifiers.
Remember, accurate interpretation of test results is crucial in preventing epoxy coating failures due to excessive moisture.
Avoiding Common Mistakes in Moisture Testing
Looking to get your garage floor professionally coated? Creative Coatings would be honored to coat your floor! Get a free quote now by calling us (320)-808-3284 or by contacting us directly on our site!
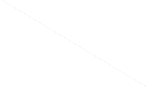
When conducting moisture tests, it’s easy to make mistakes that can skew your results. One common error is testing too soon after the concrete has been poured. Concrete needs time to cure properly before testing. If you test too early, you’ll likely get a high moisture reading that doesn’t accurately reflect the slab’s condition.
Another mistake is neglecting to account for environmental conditions. Factors like humidity and temperature can significantly impact moisture levels in concrete. Lastly, always ensure your testing equipment is calibrated correctly. Inaccurate equipment can lead to false readings.
Conclusion: Ensuring the Longevity of Your Epoxy Coating
Moisture testing is a crucial step in preparing concrete for an epoxy coating. It helps ensure the longevity of the coating and prevents potential issues like peeling and bubbling. By understanding the importance of moisture testing and how to conduct it properly, you can ensure a successful epoxy application. This will save you time, money, and potential headaches down the line.
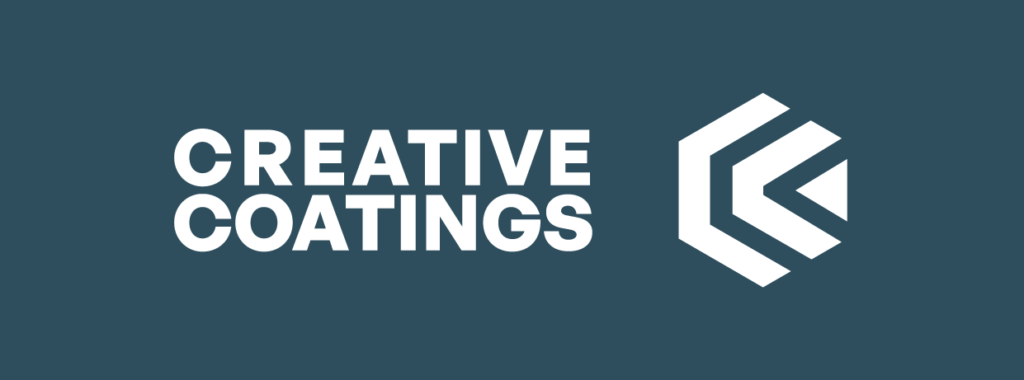